Category: Blog
December 2024: Case Power Shuttle Transmissions Rebuilt and Ready to Go!
December 2024: Hydraulic Cylinders in Stock!
December 2024: Rebuilt Hydraulic Pumps in Stock!
December 2024: Rebuilt Injection Pumps In Stock!
DECEMBER: LOOKING TO SELL?
GSES NOVEMBER 2024
GSES September 2023 Newsletter
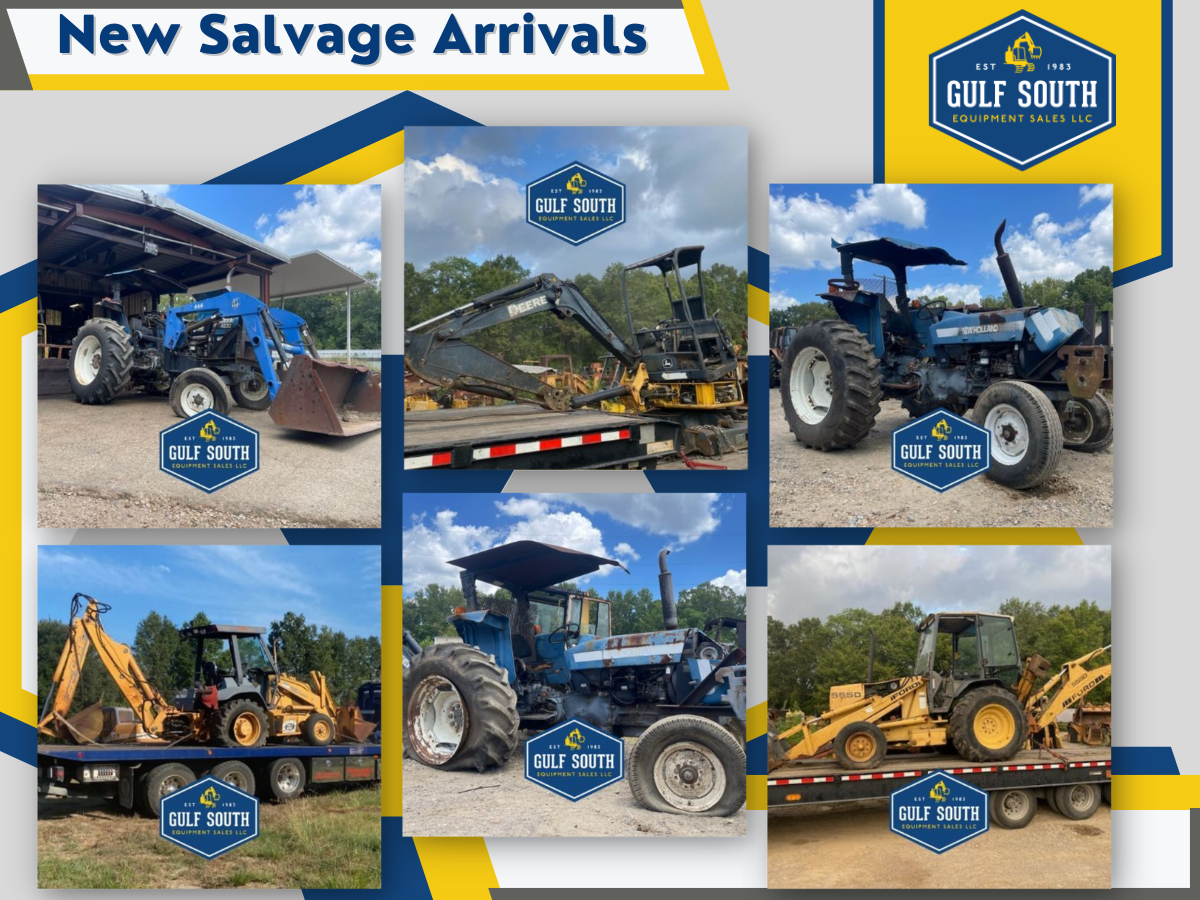
GSES April 2023 Newsletter
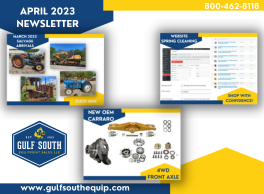
February 2023 Newsletter (January Recap, Giveaway, Catalog)
Gulf South Equipment Sales 2022 Year In Salvage
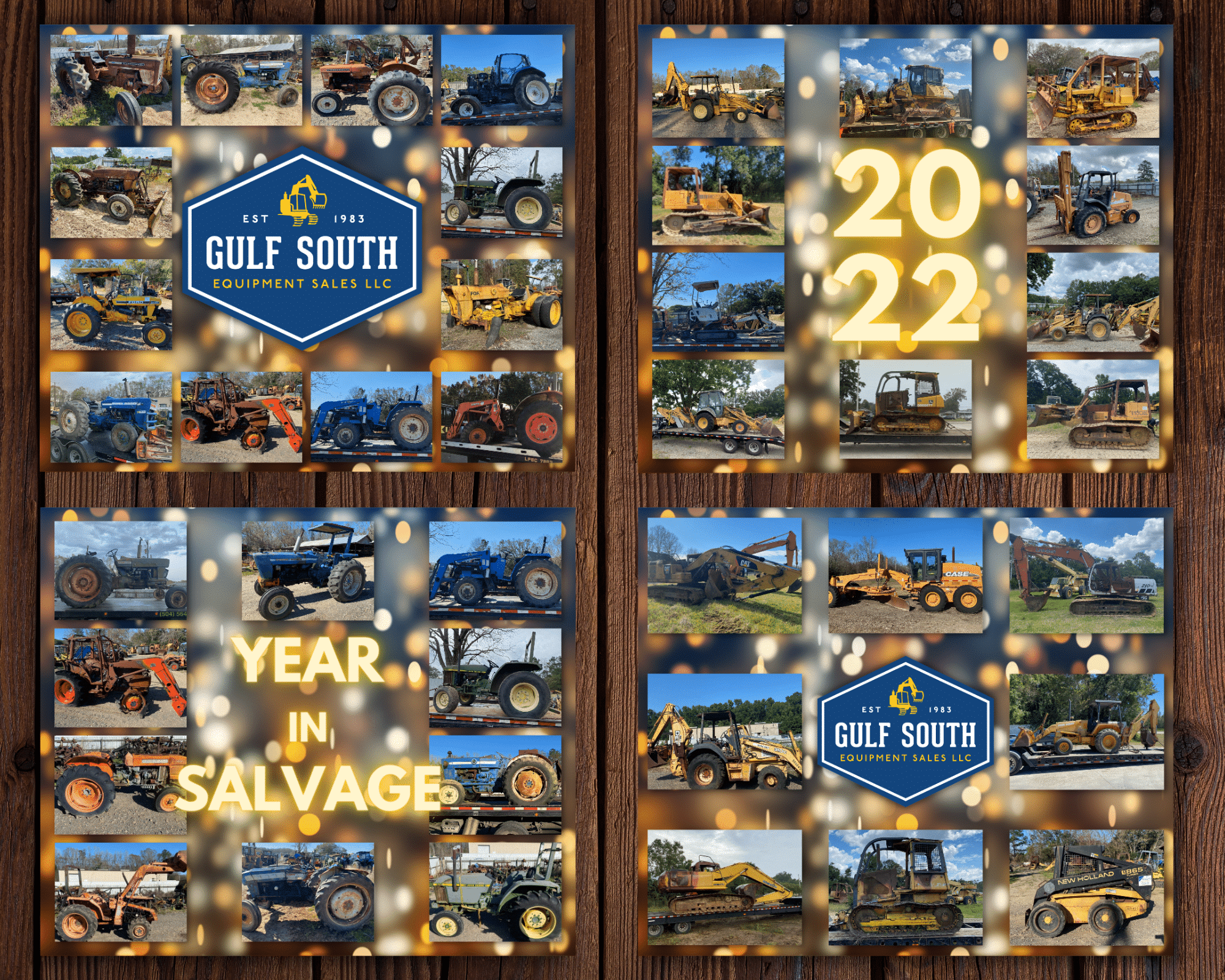
Product Tags Gallery
GSES Backhoe 101
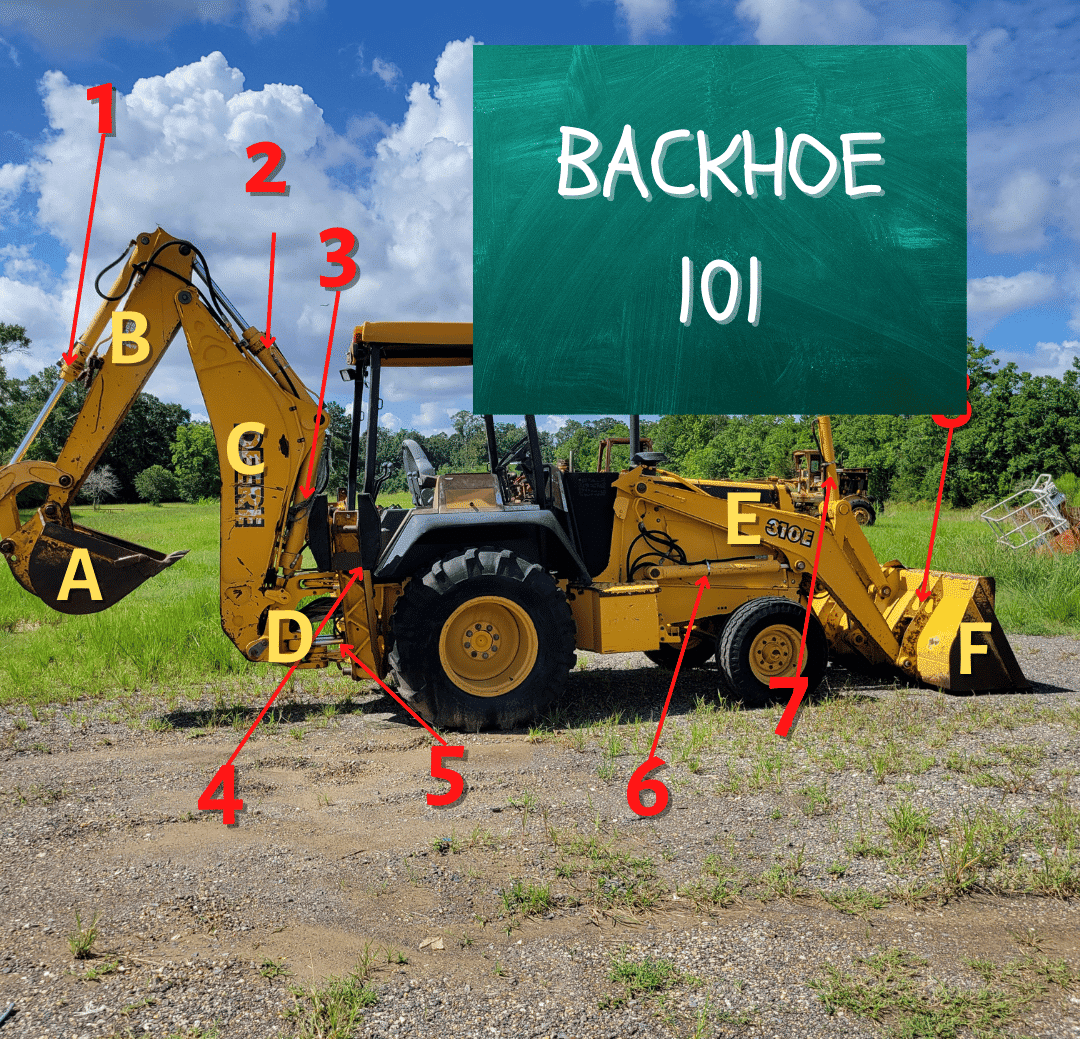
September 2022 Newsletter
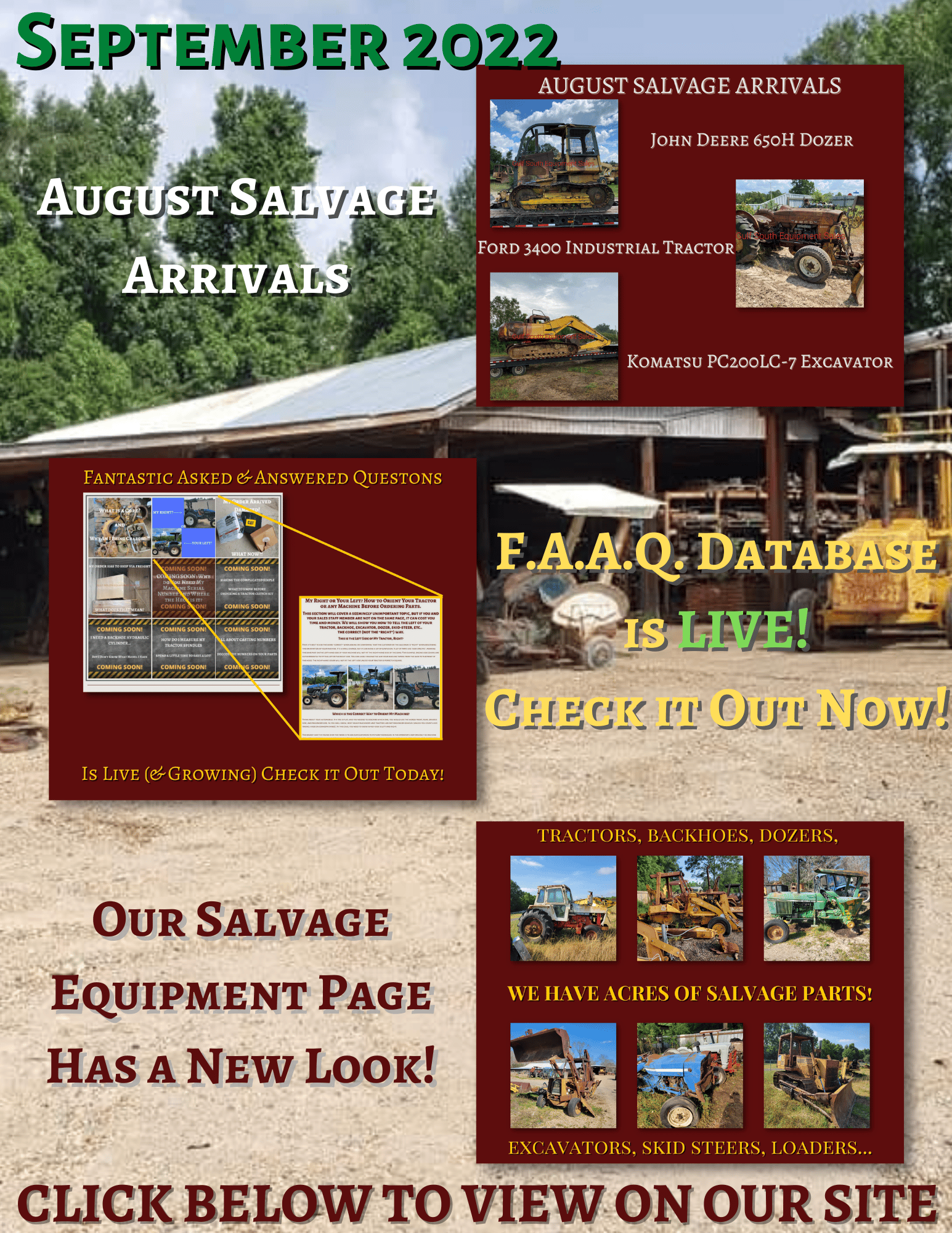
I Just Bought a Hydraulic Pump from You. Do I Need to do Anything Before Installing it?
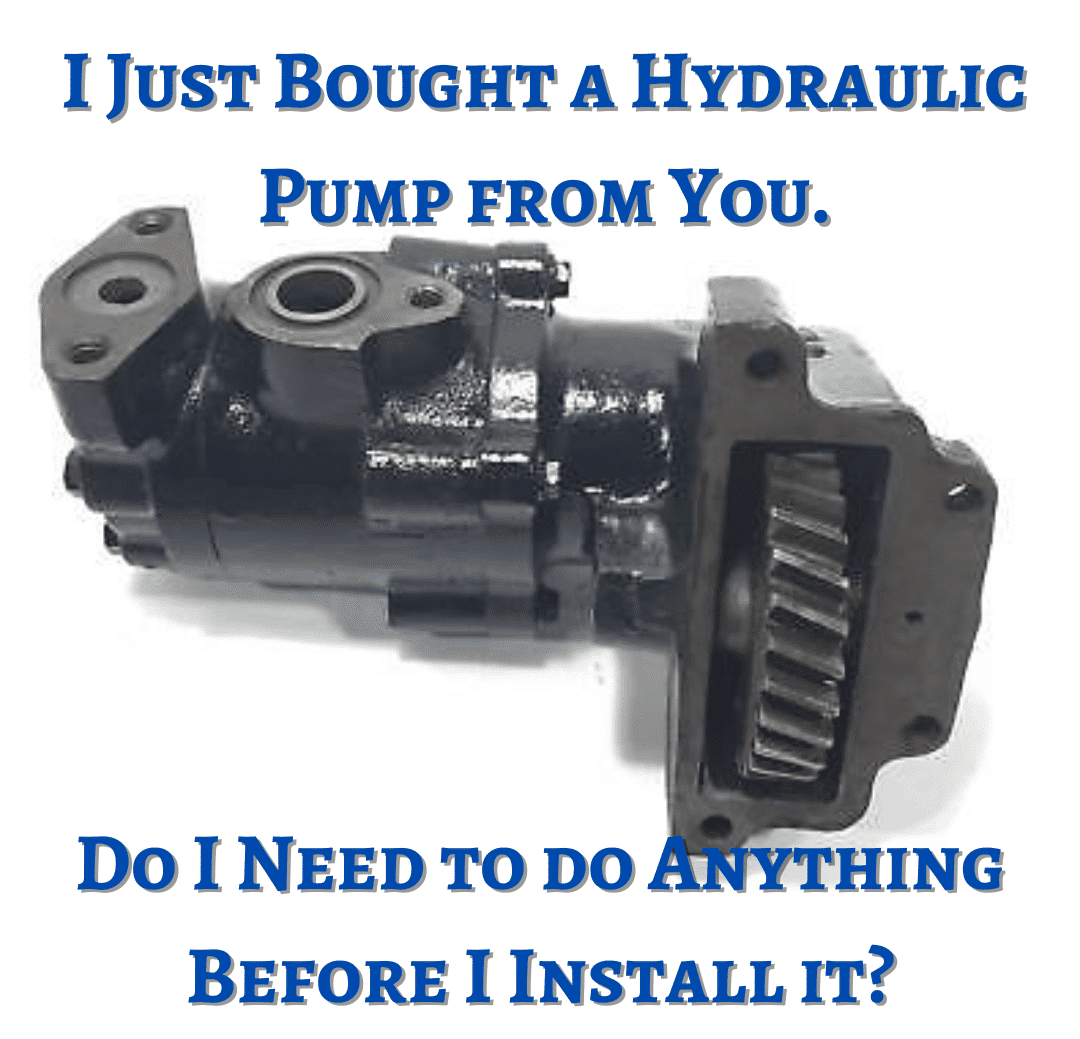
All About Casting Numbers
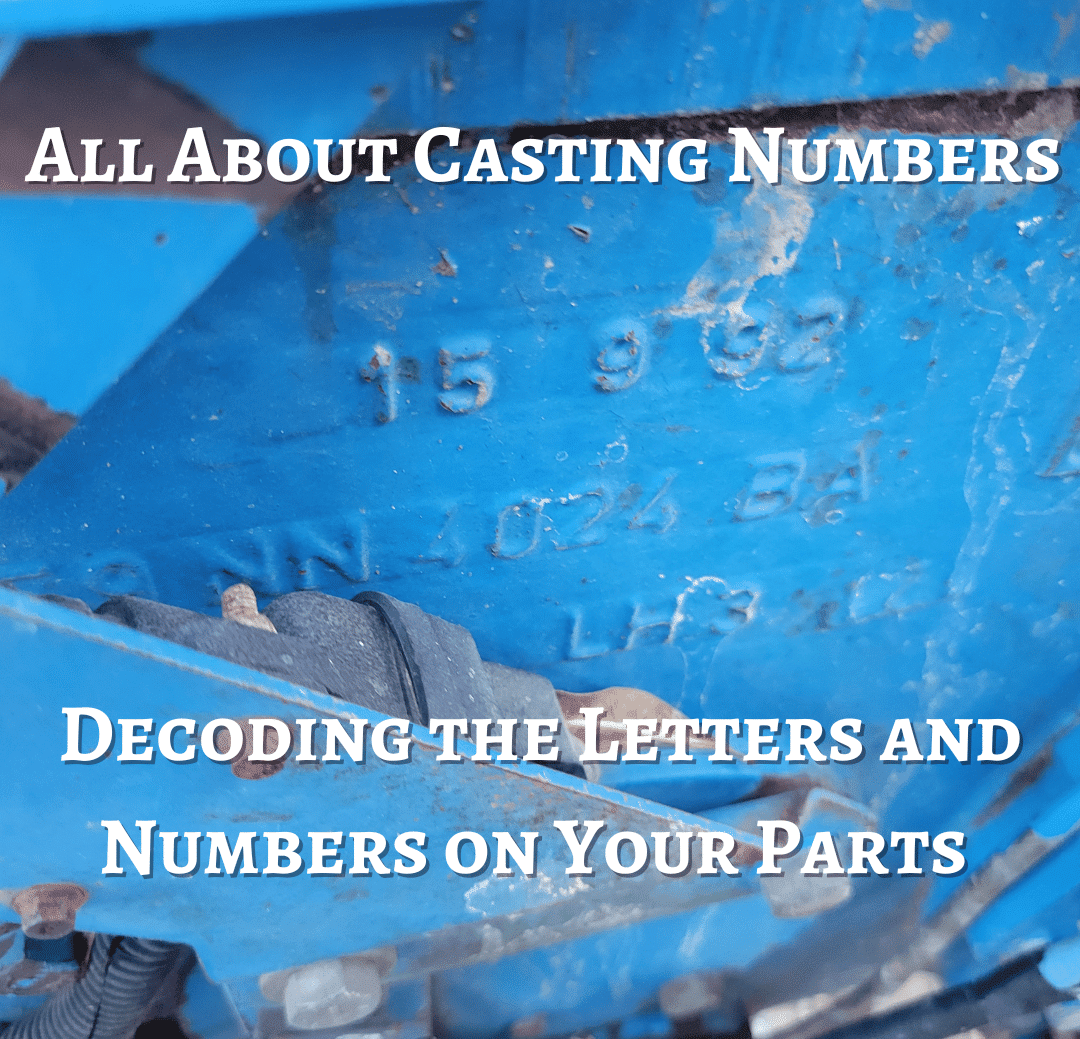
My Part Arrived Damaged! Now What?!
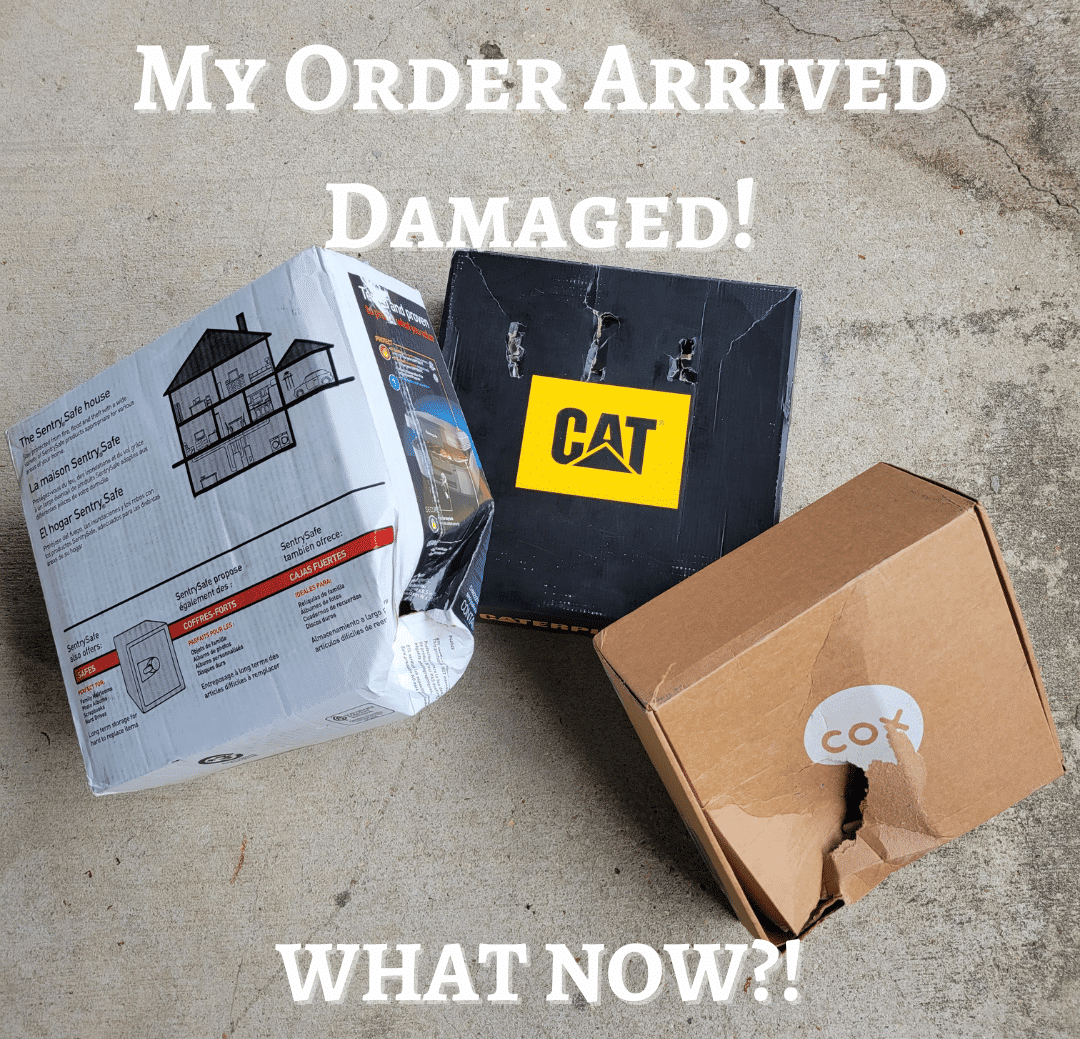
Why do You Need My Machine Serial Number and Where the Heck is it?
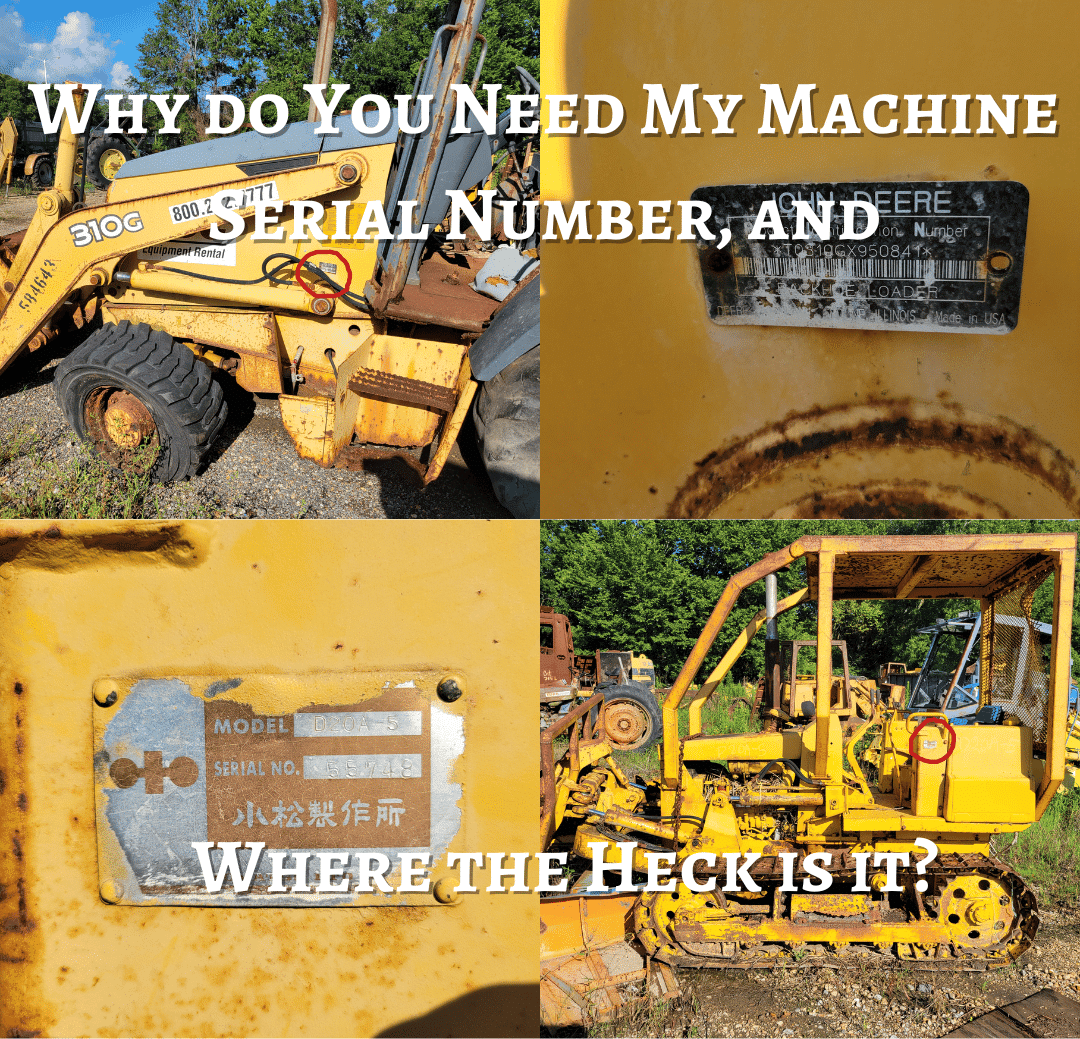